Introduction to Raymond Mill
Raymond mill is mainly composed of host machine, analyzer, fan, finished product cyclone separator, micro powder cyclone separator and air duct. The main machine consists of a frame, air inlet volute, blade, grinding roller, grinding ring and cover. Relying on the grinding roller device suspended on the plum blossom frame of the main machine, it revolves around the vertical axis and rotates on its own. Due to the centrifugal force during rotation, the grinding roller swings outward and presses against the grinding ring, causing the scraper to scoop up the material and send it to the grinding mill. Between the roller and the grinding ring, the rolling and rolling of the grinding roller achieves the purpose of crushing the material. The equipment has the characteristics of high efficiency, low power consumption, small floor space, and small one-time investment. It produces less dust than high-speed centrifugal grinders, and the operation workshop is clean and the environment is pollution-free.
The historical development of Raymond mill
In 1906, C.V. Gruber founded a machinery factory in the southern suburbs of Berlin. Using the patent he obtained in the United States, he built the first Maxecon mill and used it as coal grinding equipment for the MOABIT power station. The grinding power can reach 5TPH. Within a few years, nearly 600 grinding machines were sold, used in different grinding fields.
During the same period, BEWAG planned to build a more productive coal mill. E.C. Loesche became a shareholder and operated the Curt Von Grueber Machine Factory, and then decided to purchase the U.S. patent for Raymond centrifugal ring roller mills and produced the first generation of Raymond mill systems. Its structure is a rotating spindle with a plum blossom stand in the center of the machine. There are three or more rotating grinding rollers suspended on the frame. The rotating shaft rotates at a certain speed, driving the grinding roller to swing outward, and the grinding ring embedded in the inner wall of the cylinder is pressed down by centrifugal force. When the material enters the grinding area, it is brought to the front area of the grinding roller under the action of the plow guide vanes below the grinding roller. Since the grinding force (centrifugal force) of the slow roller of Raymond coal mill is limited by the diameter and speed of the grinding roller, grinding is only suitable for soft, low-ash and good-grinding coal materials, while German coal has a hard texture and low ash content. High, requires high grinding force, and the structure of Raymond coal mill is difficult to meet the grinding requirements, so Raymond coal mill has not been popular in Germany. The Raymond coal mill at that time was just suitable for the coal pulverization requirements of the United States, so Raymond coal mills were widely promoted and used in the United States. This is the real first generation Raymond mill
In 1925, E.C. Loesche summarized the usage characteristics and structural disadvantages of the first generation of Raymond mill, further improved the grinding structure of the Raymond mill, and developed a grinding mill with the opposite grinding principle, which was called an improved type. Raymond mill. The ventilation of this improved Raymond mill system has two methods: positive pressure and negative pressure direct blowing. This type of Raymond mill was soon purchased by American Combustion Engineering Company.
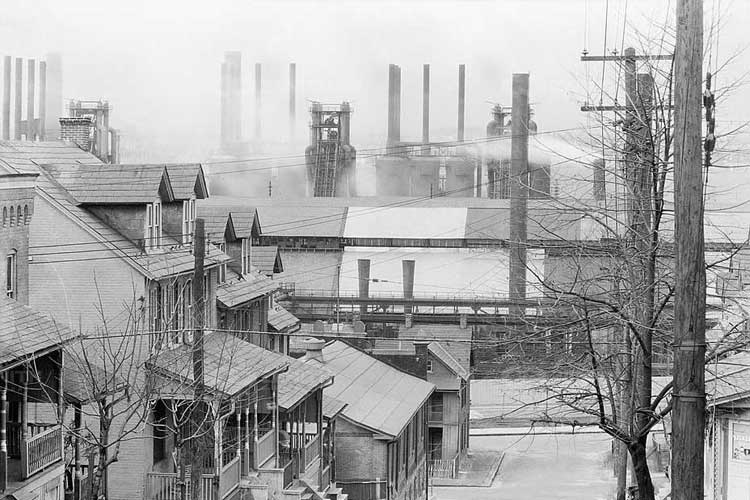
Later, because although the roller diameter of the improved Raymond mill was slightly increased, the grinding force did not increase much, the company developed a new generation of Raymond mill on this basis, called VR mill. This Raymond mill is similar to the current structure in many ways. It is worth noting that it is different from today's conical grinding rollers and flat grinding discs, but uses a cylindrical grinding roller and a grinding disc with an inclined grinding surface at an angle of 15 degrees. The grinding roller has a roll-out device similar to the current one during inspection and maintenance, and is also equipped with a protective device to prevent metal contact between the grinding roller and the grinding plate. In addition, the grinding roller can be lifted in advance before the mill is started, which can reduce the starting torque of the motor. Thereby reducing energy consumption.
In industrial applications in the United States, Raymond mills are usually used to prepare pulverized coal. The fineness of the mill varies between 250-325 mesh, and the product fineness and output can be adjusted during operation.
For a long time, the Raymond mill industry in developed countries such as North America and Europe has developed very fast and is far ahead in the entire industry market. Its development speed is higher than the average development speed of the flour milling industry, and the flour milling industry is also relatively complete. With years of technological improvements, there are more and more types and models of Raymond mills. Because of their stable performance, strong adaptability, and high cost performance, Raymond mills occupy a very important position in crushing equipment.
Grinding process of Raymond mill
Raymond mill is an integrally graded air-swept vertical pendulum mill. The vertical shaft rotates the grinding journal/roller assembly within the grinding zone. As the unit rotates, centrifugal force drives the rollers against the grinding ring. The feed enters the mill from the top of the grinding area and moves downward by gravity to the bottom of the mill. It is then lifted with a plow from the bottom of the mill to the nip area of the grinding rollers and rings where grinding occurs. The plow rotates around the central axis together with the journal and roller assembly. The ground material is discharged into the process gas stream. The airflow flows through the nozzle under the bullring, transporting the crushed material upward to the dynamic classifier. In the dynamic classifier, the coarse particles are separated and returned to the grinding area, while the qualified material leaves the mill and is collected in a cyclone separator or bag The product is collected in the dust collector.
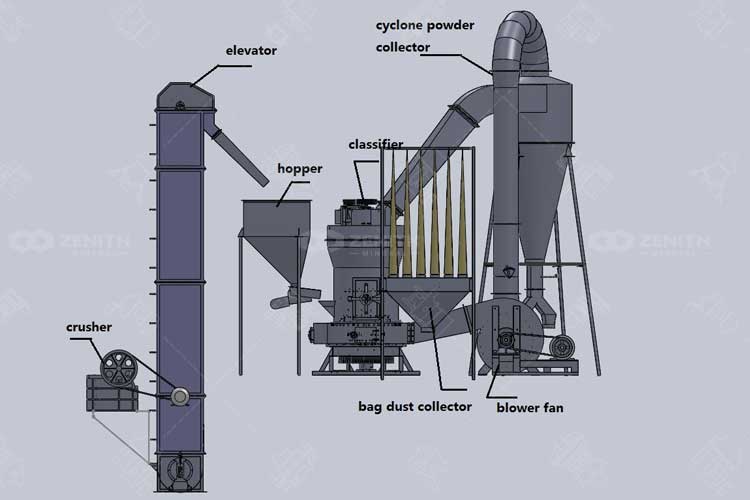
With a traditional roller mill design, during fine grinding, the classifier tailings (rejected particles) are also quite fine and can easily be entrained into the airflow. However, fine grinding roller mills are designed with a separate path for returning the coarse waste material to the grinding area, thus avoiding short circuiting of the particles. Therefore, a large number of products can be ground to 95% to 99% passing 15 to 20 microns, while other products with smaller crystal structures can be ground to 95% to 99% passing 5 to 10 microns.
Classification of Raymond mill
According to different structures and performances, Raymond mill can be divided into Raymond mill, high-strength mill, high-pressure mill, ultra-fine mill, medium-speed mill and fine powder mill. Different types The grinding mills have their own models and corresponding technical parameters. Their pressure resistance, incoming and outgoing material particle size, production capacity are different, and their scope of application is also different. Therefore, when purchasing a Raymond mill, be sure to read it carefully. , compare its models and technical parameters.
If divided according to the application range, it can be divided into activated carbon Raymond mill, heavy calcium Raymond mill and white ash Raymond mill. The activated carbon Raymond mill has been updated using advanced new technologies. Its various technical indicators have been greatly improved, and its main technical indicators are in a leading position. It is not only suitable for processing activated carbon materials, but also can handle various non-flammable and explosive materials with humidity within 6% such as talc and dolomite. The fineness of the finished product can be between 0.18-0.038mm (80-400 mesh) Arbitrary choice.
The heavy calcium Raymond mill is a technological innovation based on the ordinary mill. All technical indicators have been greatly improved compared with the traditional mill. It is a new type of grinding equipment with high efficiency and energy saving. It is suitable for grinding limestone, fluorite, zeolite and other materials. It is especially suitable for grinding heavy calcium materials. Its grinding rate of heavy calcium can be as high as 1.5 times that of other mill materials.
White ash Raymond mill is an emerging grinding equipment with the latest technology. This product is suitable for grinding white ash of various properties and has the advantages of grinding rate, high product quality and high output. It is precisely because of the emergence of white ash Raymond mill that the user's demand for fine powder materials has improved.
Industrial applications of Raymond mill
Raymond mill is a high-efficiency grinding equipment that can grind various materials into fine powder. It is widely used in mining, metallurgy, chemical industry, building materials and other industries, and is especially suitable for grinding various ores, cement, coal, coke, limestone and other materials. It adopts advanced high-pressure suspension grinding technology, which has compact structure, easy operation, high grinding efficiency, high particle size control accuracy, energy saving and environmental protection. The development history of grinding mill is very long, and the manufacturing process and technology are constantly upgraded and optimized, becoming more and more advanced.
- In the mining industry, Raymond mill is often used in the grinding and grinding process of ore. Through Raymond mill, the ore can obtain finer particle size to facilitate subsequent beneficiation and flotation processes.
- In the chemical industry, Raymond mill is often used for grinding and mixing chemical raw materials. Through Raymond mill, chemical raw materials can obtain more uniform particle distribution and improve product quality.
- In the building materials industry, Raymond mill is often used for grinding and grinding materials such as cement and gypsum. Through Raymond mill, materials can be obtained into finer powder to improve the performance and quality of building materials.
- In the metallurgical industry, Raymond mill is usually used in the grinding and beneficiation process of metal ores. Through Raymond mill, metal ore can be obtained into finer particles, making it easier to beneficiated and refined.
- In addition, Raymond mill is also widely used in ceramics, cosmetics, food and other industries for the grinding and processing of granular materials.
Advantages of Raymond mill
- The grinding pressure is large and the grinding efficiency is high;
- It has strong adaptability to materials, can continuously produce small amounts, and has high long-term production capacity.
- The structure is simple, sturdy and reliable in operation. The grinding roller and grinding ring have long service life and are wear-resistant and durable;
- The particle size control accuracy is high, and the particle size of powdery materials can be controlled freely; the crushing ratio is large, up to more than 300, and the fineness of the grinding product can be easily adjusted.
- Can be adapted to operations under various circumstances. It can be used both dry and wet, and drying and powdering can be combined at the same time.
- It has good sealing performance and can be operated under negative pressure. It prevents dust from flying. The powder production capacity is large, which saves a lot of manpower and material resources for large-scale grinding operations.
Maintenance and maintenance of Raymond mill
- Regularly clean impurities and dust inside and outside the equipment, especially grinding discs, grinders, fans, pipes and other parts. Check and ensure that each lubrication point is adequately lubricated with oil or grease to maintain normal lubrication of the parts.
- Regularly check the wear of the grinding disc and grinder, and replace them in time according to the degree of wear. Use wear parts with better wear resistance to extend their service life.
- Regularly check the transmission system, including belts, gears, drive shafts, etc., to make sure they are not loose, worn or damaged. Adjust or replace severely worn transmission parts to ensure normal transmission.
- Regularly check the fan impeller and bearings to ensure they are operating properly. Clean and inspect the exhaust system to ensure smooth ventilation and prevent blockage from affecting fan performance.
- Regularly check electrical systems, including cables, connectors, switches, etc., to ensure they are safe and reliable. Check the insulation of the motor to ensure that the motor is working properly.
- Check the air tightness and seals of the equipment to ensure pressure balance inside and outside the system to prevent dust leakage.
- Monitor the temperature of the equipment while it is running to ensure that the equipment is not damaged due to overheating. Check the cooling system regularly and clean the cooler to ensure good cooling effect.
- For Raymond mills with automated systems, regularly check and calibrate sensors, instruments and controllers to ensure their accuracy and reliability.
- Maintenance records should be kept to record the maintenance history of the equipment, including maintenance date, maintenance content and parts replacement.
New technology of modern Raymond mill
Introducing advanced digital control systems and automation technology to achieve a more precise and stable grinding process. Utilize sensors, data collection and remote monitoring to achieve real-time monitoring and remote control of equipment status.
Artificial intelligence and machine learning algorithms are used to optimize the grinding process by analyzing the operating data of the grinding mill. Predictive maintenance: Use machine learning algorithms to predict possible equipment failures to perform maintenance in advance and reduce downtime.
Use advanced wear-resistant materials and coating technology to improve the wear resistance of grinding mill parts and extend their service life. New ceramic materials are used to improve the wear resistance and corrosion resistance of wearing parts.
Introduce efficient motors and frequency converters to improve energy utilization and reduce energy consumption. Combined with energy recovery technology, part of the waste heat or energy can be used in other equipment or production links.
Through technologies such as simulation and computational fluid dynamics, the structure and grinding process of the grinding mill are optimized to improve grinding efficiency. Use computer-aided design and simulation to optimize the layout and motion trajectory of the grinding media.
Introduce more environmentally friendly cooling systems and lubrication systems to reduce environmental impact. Use a closed grinding system to reduce the emission of dust and particulate matter.
Sustainability throughout the entire life cycle, including design, manufacturing, use and disposal stages. The equipment is designed for disassembly and easy recycling to promote circular economy concepts.
Explore new grinding media to improve grinding efficiency and reduce energy consumption. Develop new grinding processes, such as ultrasonic grinding, to suit different types of raw materials and grinding needs.
Raymond mill’s environmental protection concept
Use efficient motors and advanced power control systems to reduce power consumption. Introducing technologies such as frequency converters to enable equipment to automatically adjust its operating speed according to actual needs to avoid excessive energy consumption.
Use environmentally friendly materials and coatings to reduce the wear and corrosion resistance of parts, extend their service life, and reduce replacement frequency.
Optimize cooling systems to reduce water requirements. Promote circulating water systems to achieve multiple uses of water.
Through sound insulation design and vibration reduction devices, the noise and vibration generated during equipment operation are reduced, and the interference to the surrounding environment and workers is reduced.
Use environmentally friendly lubricating oil or grease to reduce pollution to soil and water sources. Check and replace lubricants regularly to keep equipment properly lubricated.
Implement the concept of cleaner production and reduce pollutant emissions during the production process through technological innovation, equipment improvement, etc. Promote efficient, low-pollution methods for grinding processes.
Continuously introduce new environmental protection technologies and R&D innovations to improve the environmental performance of equipment. Actively participate in industrial research and cooperation to promote the development of the entire industry in a more environmentally friendly direction.
With the continuous development of the powder industry, the market demand for Ramon grinders is also increasing. Raymond grinding machine is the main equipment in my country's grinding industry. In order to adapt to the needs of different application fields, it is an inevitable trend to develop in the direction of "high reliability, energy saving, high precision, and automation".