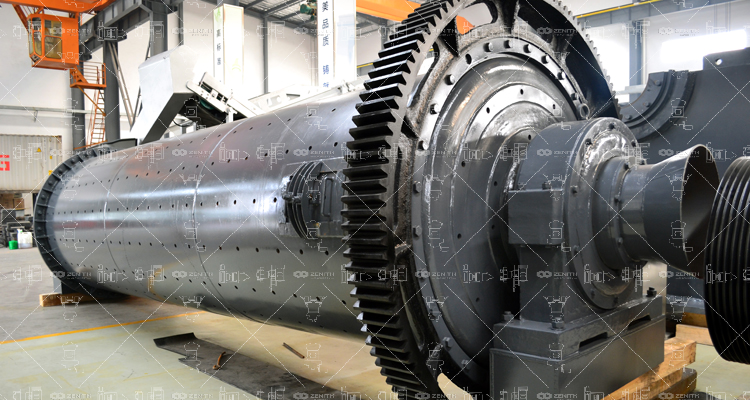
1. Using cement grinding aids
Adding a small amount of cement grinding aid during the grinding process can improve the grinding efficiency, which is beneficial for the high-quality, energy-saving, and high-yield of the ball mill. Since the use of cement grinding aids by a certain enterprise, the increase in production of ball mills has remained stable at over 10%, and the electricity consumption per unit production can be reduced by about 10%. The addition of mixed materials can be increased by about 5%.
2. Control the moisture and temperature of the incoming grinding materials
The moisture content of the mixed materials entering the factory should be strictly controlled and carefully reviewed, and the temperature of the ground materials should be strictly controlled within the process requirements. To ensure stable output of the grinding machine, the comprehensive moisture content of the incoming material should be ≤ 1%.
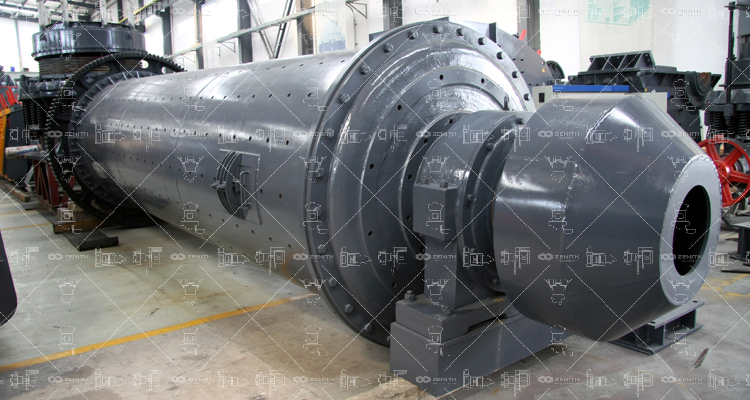
3. Control the grindability of incoming materials
To ensure the grindability of the raw materials, firstly, it is necessary to produce clinker with good grindability as much as possible, and secondly, it is necessary to choose a mixture with good activity and grindability.
4. Control the ventilation inside the mill well
To ensure a virtuous cycle of ventilation inside the mill, all ventilation ducts should be regularly cleaned under normal production conditions. The dust collector should be cleaned once a week, and when the warehouse is full, it should be stopped for cleaning. The ventilation of the powder selection machine should be adjusted reasonably to ensure the stable improvement of the mill's output and quality.
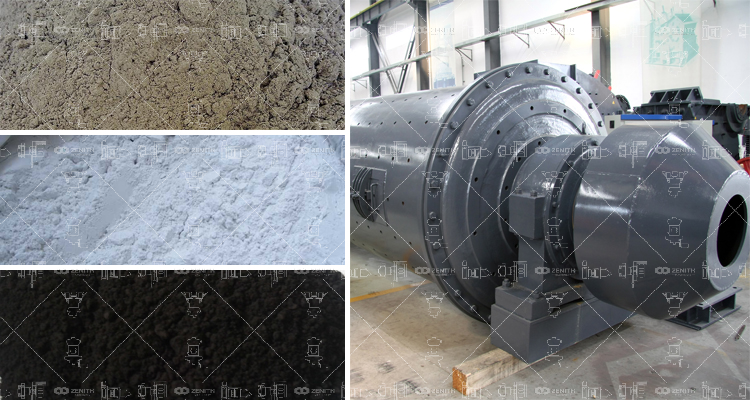
5. Timely adjustment of grinding material grading
One is to increase the loading capacity of the ball section appropriately when the equipment configuration allows; The second is to supplement the specifications and quantity of grinding bodies, mainly depending on the material of the grinding body, the output and quality of the grinding machine, and the operating time; The third is to determine the quantity of supplementary grinding materials based on the measured consumption of grinding materials per ton of product; The fourth is to supplement the grinding body based on the changes in the current of the grinding machine, the level of grinding sound, the output and quality of the grinding machine in daily production; The fifth is to regularly inspect the damage of the grinding body in the warehouse. When there are many damaged steel balls, the warehouse should be cleared and re graded. In general, 3-4 graded balls can be used for one silo, and 2-3 grades are sufficient for fine grinding silos. The clearance of the ball warehouse is particularly important, and the clearance period should be determined based on the quality of the ball section, and the longest should not exceed 6 months.
6. Control the fineness of finished products
In production quality control, the control of cement fineness mainly adopts sieve analysis method and cement specific surface area method. The sieve residue of 0.08mm should be controlled within the range of 2.5% to 3%, and the specific surface area of cement should be controlled within the range of 360 to 375 ㎡/kg.
.jpg)
7. Strictly control the particle size of incoming grinding materials
One is to adopt the method of "breaking more and grinding less" to keep the particle size of the incoming materials below the internal control standard; The second is to control and track the particle size of the mixed materials, truly achieving the rational feeding of various material particle sizes into the mill.