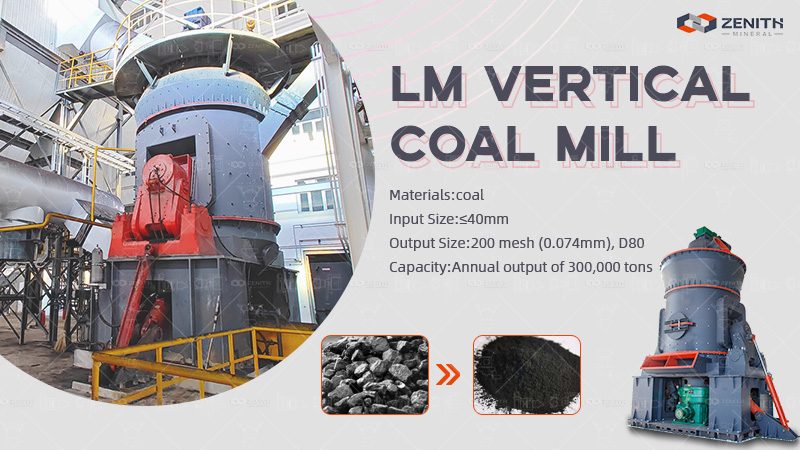
Magnesium and magnesium alloys, as important light metal materials, have advantages such as light weight, high strength, good thermal conductivity, and corrosion resistance. Therefore, they have a wide range of applications in industry, military, aerospace, medical and other fields, and are known as "the green engineering material with the greatest development and application potential in the 21st century" Green engineering materials for power. When using dolomite as a raw material to smelt magnesium metal, the first step is to send dolomite into a rotary kiln for calcination to obtain calcined white. During this process, the rotary kiln often uses coal powder with high combustion rate, clean and environmentally friendly, and good stability as fuel, which fully meets the production needs of continuous operation of rotary kilns, has a wide range of applications in solid fuels for rotary kilns.
The user is a large magnesium smelting enterprise specializing in the mining and processing of dolomite. In the rotary kiln calcination process, their fuel supply system adopts the complete set of Shanghai Zenith LM vertical coal mill equipment. The entire coal powder preparation production line is designed by Zenith Company Fully considering the user's on-site situation, the layout is reasonable and compact, with a small footprint and low investment costs. The Shanghai Zenith LM vertical coal mill, as the main equipment of the coal powder preparation production line, provides sufficient and high-quality coal powder fuel for the calcination process of dolomite in enterprises,Winning customer satisfaction and praise for its energy-saving, environmentally friendly, and safe features.
.png)
The production process of clean coal powder preparation mainly involves the raw coal passing through a grid screen and falling onto a large angle belt conveyor or hoist. After being iron removed by an electromagnetic iron remover, the belt conveyor or hoist sends the raw coal into the raw coal bin for storage. The powder production system is waiting for After starting, open the bottom rod valve of the raw coal bin, start the sealed metering belt coal feeder, and the raw coal enters the LM vertical coal mill for drying and grinding. The hot air or exhaust gas from the hot blast stove is drawn by the system fan and enters the vertical coal mill, where it is mixed with the coal inside the mill After sufficient heat exchange of the ground raw coal, the coal powder is picked up and sorted at the separator. The coarse coal powder with unqualified fineness is re dropped onto the grinding disc for grinding. The qualified coal powder enters the explosion-proof gas box pulse dust collector with the airflow and is collected. It is then discharged through the sorting wheel Enter the coal powder silo. The impurities in the raw coal, such as some coal gangue and metal blocks, are removed from the mill through the air ring and slag outlet. Throughout the entire process, a CO-O2 online analysis system is installed. When processing coal with high volatile matter, nitrogen protection and CO2 automatic control can be set up Fire extinguishing systems and other safety measures.
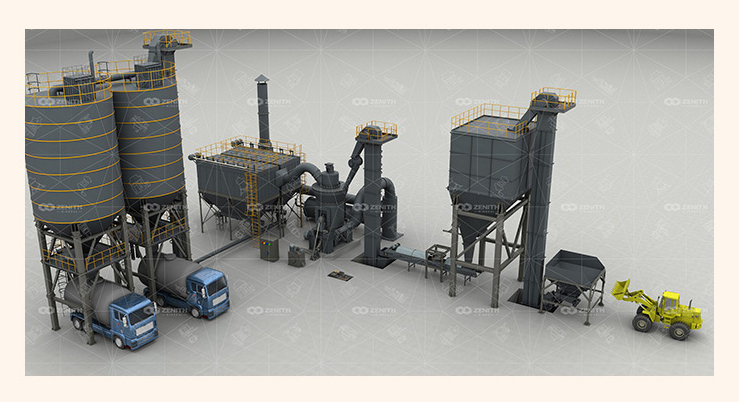
Advantages of Shanghai Zenith products:
1. Leading technology, low investment cost
2. It integrates crushing, grinding, drying, powder selection, and transportation, with a compact layout that can be arranged outdoors and low investment costs.
3. The equipment is easy to operate, adopts a thin oil automatic forced lubrication system, and is equipped with a hydraulic roller flipping device. During maintenance, the grinding roller can be flipped out of the machine by the hydraulic device. The maintenance space is large, the maintenance is convenient, and the operating cost is low.
4. Adopting five level safety and explosion-proof measures, the design is safe and reliable, and meets national and industry parameter specifications.
5. Hot air can be used to transport materials, and the inlet air temperature can be controlled according to the moisture content of the material. Materials with a moisture content of up to 15% can be dried and ground, while those with a moisture content of less than 1% can be dried and ground.
6. Special grinding roller and disc structure design, and the grinding roller adopts hydraulic automatic pressure device, with a large grinding area, high grinding efficiency, and large output.
7. A professional technical service team provides users with design, supply, and installation general contracting services, integrated comprehensive solutions, and is worry free and labor-saving.